This week, we've finished up assembling our yoyo's! All of our productions runs were finished last week, but we needed a bit more time to order the stickers and assemble everything.
Here's a look back at everything:
Thermoform:
Here is a picture of the thermoformed cover. Right after thermoforming, the piece looks like as below.
The piece is subsequently cut to yield the clear covers that will fit in the yo-yo body.
Key features: The key features are the diameter of the dome, the height of the dome, and the outside cut diameter. The diameter of the dome is determined by the webbing between the pins and the dome, because webbing increases the diameter, and the dome may not be able to fit inside the retaining ring. The outside cut diameter depends on the die used to cut the covers from the thermoformed sheet. It also depends on the protrusion of the pins, which align the cutting die - if there is too much webbing, the pins will not be substantial enough to align the piece to the cutting die. Thus, the amount of webbing is a key feature that determines the quality of the piece.
Successes: We were able to decrease the webbing between the dome and the pins by increasing the heat time and oven temperature. This, however, caused a longer production time, from the increased heating and cooling times, but the quality of the piece was much improved. In our disturbance, we introduced shorter heating times, and the introduction of more webbing caused an increase in the diameter of the dome. This is seen below in the figure.
This is one of the "disturbance" thermoformed pieces, which has a shorter heating time. As a result, there is more webbing. When it is cut out, the diameter is much larger and the height of the dome is decreased. This is seen below.
This is a comparison of the distaurbance thermoformed piece (on the left) and the regular theormoformed piece. The disturbance piece has an obviously larger dome diameter and a less defined corner, which would cause fitting problems.
We successfully reduced webbing by increasing oven temperatures.
Opportunities for improvement: Currently, some of the pieces are speckled with bumps caused by dust particles which adhered to the clear particles while the plastic was heated and thermoformed. Although precautions were taken in cleaning the mold and blowing dust off the plastic, this did not improve the quality, and dust continued to stick to the plastic from the static when the plastic was peeled. One good improvement would be to increase the quality of the piece by getting rid of the dust.
Retaining Ring:
Key features:
The most important dimensions of the retaining ring are the snap fit diameter (the inner diameter) and the width of the snap fit. If the two did not match the yoyo body’s, the process would need to be changed and the retaining ring redone.
Successes:
Luckily for us, the final retaining ring did fit perfectly into each of the yoyo bodies, and even gave a satisfying snap each time during assembly! However, it took several tries to get there.
We initially had issues with the retaining ring not coming cleanly off of the molds when the ejector pins tried to push the part off. After changing everything from the pressure profile to the cooling time, it was determined that the mold would have to be remachined since the gates were just not strong enough (read: too thin) to help push the part off.
Unfortunately, the gates could not simply be made deeper because they were already on the cusp of cutting too deeply into the retaining ring pocket. Instead, we decided to drill an outer ring, allowing us to add the maximum number of gates possible.
Once the part was consistently ejecting from the molds, the pressure profile was tweaked until we eliminated flash!
Opportunities for Improvement:
Ideally, we wouldn’t have had to snip the gates off of every retaining ring before the final assembly -- not just in the interest of time, but in terms of aesthetics as well. Even the best-snipped ring still had visible blemish marks if you look closely enough.
Letter Board
Key Features:
This part was mostly for aesthetics thus there are no critical dimensions. However, important features include the look of the letters, filling the mold properly, and pinching the molded parts well.
Successes:
The letters went through several iterations before they were ready for final production. Initially the letters were at a height of 0.083 inches, however, releasing these parts from the mold was difficult even with the use of a mold-releasing spray and ejector pins. Thus the part was reduced to 0.05 inches in height. This change combined with ejector pins and mold-releasing spray made it possible to run these parts in fully automatic during final production.
The board initially had filling problems. The channels were only 0.025inches in height and thus impeded the plastic flow from filling the mold. Simply increasing the channels to 0.05inches allowed for easy fill.
In the final mold we were able to control the filling of the mold and pinching of the parts well as to minimize parts moving and keep the plastic injected into the last mold from covering up the board and letters but still fill them properly. This took many iterations of optimizations which included better orientating the gates on the final mold and adding reinforcements to the letters so they would not move as much in the final mold.
Opportunities for Improvement:
The letters and board still shift in the direction of plastic flow in the final mold. There are a few possible solutions to fix this. One would be to move the gates on the final model so that they open at the corners of the letters rather than below them. Another would be to make the board’s bottom row of squares a bit thicker so they have more strength (but not too thick to be overtly noticeable). Also the letter reinforcements could be better optimize to withstand the force of the flow.
Body:
Key features:
The body is actually formed from 3 molds, two cores and one cavity. This allows one side of the body to have a flat internal cavity, while the other body piece has a small plastic axle to spin the “wheel of fortune” disk. The body had to have a rounded exterior to slide past the string, while press-fitting to the ring and letterbox parts.
Here’s an image of one of the body core molds.
Successes:
The snap fits were remarkably consistent and did not require any remachining with the ring. I was also concerned about the spinner mount, because it was a long thin feature located far from the gate. Although the spinner mount was slightly rounded at the top, it was functional.
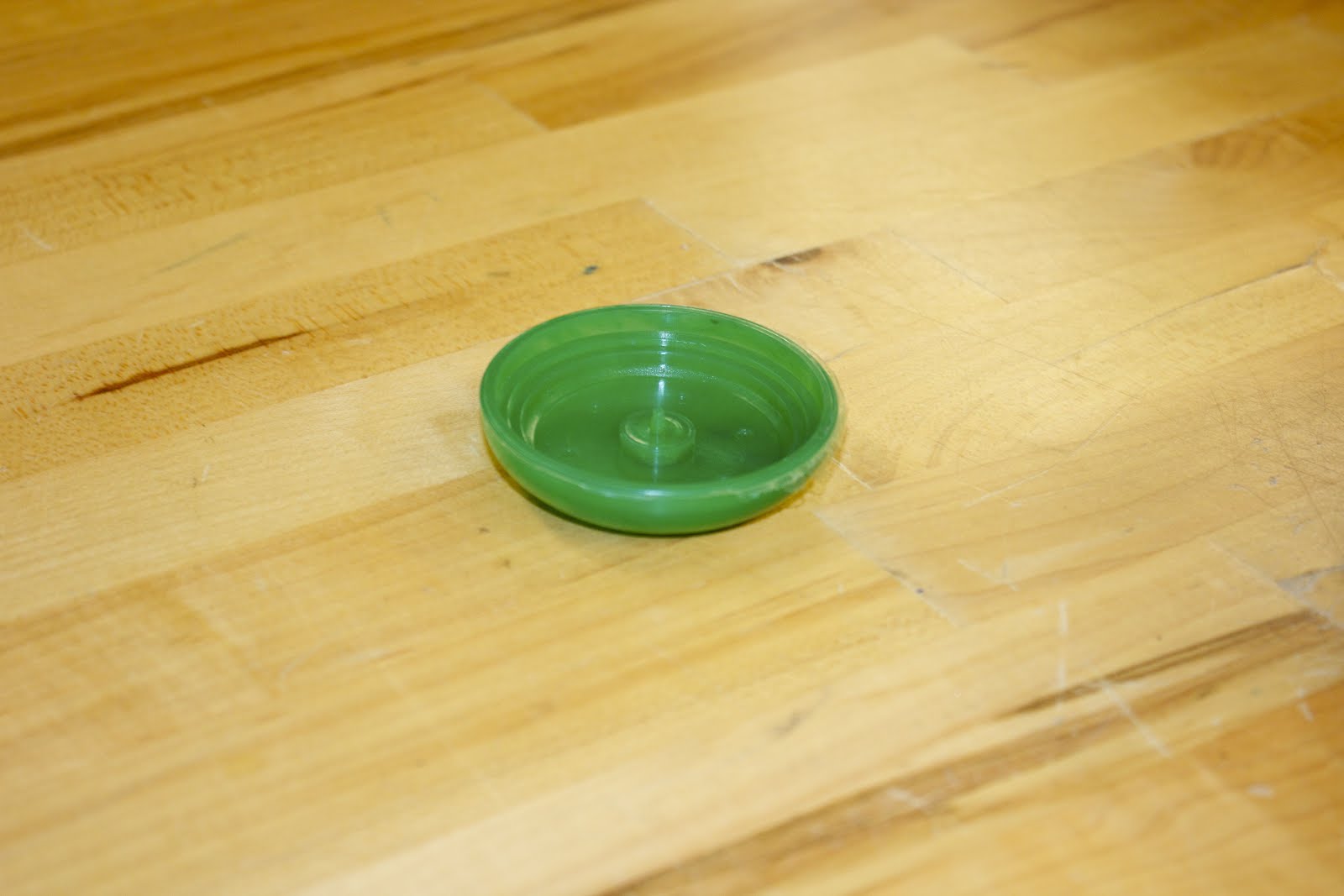 |
An early part, complete with flashing. |
Opportunities for Improvement:
We encountered challenges with edges of the part, as plastic leaked out of the parting line during the cycle. The part is also large, and it didn’t cool completely before it was injected, leaving injector pin deformations. We solved these by increasing the clamping pressure and slightly reducing the shot volume. We also increased the cooling time, which reduced the ejector pin marks.
A body family tree, from first part to latest.
Table of specs comparing YY design specifications and measured specifications:
Thermoform Diameter
Design spec
|
2.100±0.005”
|
Measured spec
|
2.07942”
|
Explanation: There was no significant shrinkage in the measured spec of the thermoform - this could be because of small defects in machining or thin spreading of the plastic during thermoform. Overall, it was insignificant, and functionality was conserved.
Body with Spin Stick Snap Fit Diameter
Design spec
|
2.346±0.000/0.005”
|
Measured spec
|
2.29384”
|
Explanation: When injection molding, the parts produced by the mold shrink due to . Although we attempted to account for shrinkage by measuring previously injection molded parts, we were unable to completely predict the effects of shrinkages. However, the parts still snapfit together well, so functionality was conserved.
Body without Spin Stick Snap Fit Diameter
Design spec
|
2.346±0.000/0.005”
|
Measured spec
|
2.2908
|
Explanation: When injection molding, the parts produced by the mold . Although we attempted to account for shrinkage by measuring previously injection molded parts, we were unable to completely predict the effects of shrinkages. However, the parts still snapfit together well, so functionality was conserved. In addition, the body without spin stick had more shrinkage than the body with spin stick (as seen in the reduced measured spec) - this is because the spin stick acts to cool the body, resulting in less diameter shrinkage for the body diameter.
Retaining Ring Snap Fit Diameter
Design spec
|
2.3±0.005”/0.000
|
Measured spec
|
2.29933
|
Explanation: The retaining ring came out a little smaller than intended in the actual production run because injection molded parts shrink. This is due to the fact that the part contracts during cooling due to the part’s polymer properties. However, this was still okay because the body also shrunk during its production run.
Summary of finding in Paper Deliverable 4 for retaining ring:
We chose the subgroup size to be five parts because it divides evenly into the 100 parts that were produced and is small enough to still provide a descriptive graph shape of the production:
Upper Control Limit = 2.301 in.
Lower Control Limit = 2.298 in.
The disturbance midway through the production run of the retaining ring did not produce a notable step change. For the disturbance, the pressures in the bottom row of the injection hold pressure profile were all dropped by 100 psi. It’s possible that the pressure change was too minor to produce a noticeable effect on the injection molded piece since the top half was still kept constant.
Process Capability:
Cp = = 6.672 x 10-6
Cpk = 16.18
According to this our process is not capable but 100 samples is also pretty low for understanding the process. With more optimization we and samples we could make this process more cabaple.
Here is the link to the paper deliverable.